Welcome
Welcome to Turbine Dynamics, a company specialising in the design, development and manufacture of down hole alternators and related electronic instrumentation for the Oil & Gas industry.
Turbine Dynamics was founded to exploit its portfolio of international patents in the field of Mud Alternators, EM Telemetry and Mechanical Actuation and is proud to announce the completion of its corner stone product; the World’s first Closed Loop Mud Alternator. See the link below for further details about this ground breaking invention.
Turbine Dynamics other interests include a 100 Watt EM Telemetry tool which will exploit the unique characteristics of the Closed Loop Alternator to produce the most powerful EM tool currently available.
Third in this series of engineering precedents is the design of a precision actuator for down hole position, speed and torque control. This mud driven rotary machine is small, light, extremely reliable and can easily be used for a variety of steering and/or surveying functions.
Please call or e-mail for more information or to discuss any other these products and developments.
Closed Loop Turbine
Turbine Dynamics alternator uses unique electromagnetic technology that guarantees the machine is able to automatically correct and regulate itself against all changes in load and flow conditions. Unlike conventional open loop alternators, the output voltage from our alternator remains constant against flow, guaranteeing unparalleled levels of performance and down hole reliability from this instrument. One of the key failure mechanisms associated with open loop alternators is the high voltage and high thermal stress they cause to down stream electronic regulators. By removing this high voltage and thermal stress at source, our alternators automatically improve the life time and reliability of any down stream electronics, be they customer’s instrumentation or our own.
Turbine Dynamics alternator has also been designed to be field friendly requiring minimum effort and time to inspect between jobs. The rotor is a one piece assembly that slides off the stator quickly and easily to allow the bearings and the impeller to be inspected and changed if necessary. The rotor is the only moving part of the whole instrument minimising component count and maximising reliability. Designed for 4¾” OD collars, the tool is only 55mm x 1300mm and requires only one impeller for all flow rates between 100 & 600 GPM. The tool is also very light, weighing only 14Kg and is easily managed by one man.
Customers can specify their own primary and secondary output voltages. The primary DC bus is typically 25V – 35V intended to complement or replace Lithium battery stacks and is the main source of 100 Watts available from the alternator. A series of secondary instrumentation voltages can also be supplied, e.g. 3V3 or 5V for down hole processors and ±12V or ±15V analogue supplies. Please call to discuss or for additional technical information.





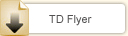
EM Telemetry
EM Telemetry is the future of efficient Oil field development and production and Turbine Dynamics next engineering project is to produce a 100 Watt EM Tool using its Closed Loop Alternator as the power source for this exciting development. Existing EM Telemetry tools use batteries for their primary power which limits the range and life of the EM Tool. Whilst careful battery management extends the down hole life of the Tool, this is at the cost of intermittent data and potential drilling errors causing high drilling resistance, poor rate of progress and reach. By substituting our 100 Watt Closed Loop Alternator, we will create an EM Tool that can be run continuously, generating a constant stream of steering data that will minimise drilling errors and maximise the reach of modern horizontal drilling capability. Please call to discuss or for additional information.
Actuation Tools
In both exploration and production environments mechanical control is fundamental to the successful development of an oil and gas reservoir and manifests itself as either position, speed, acceleration or torque or a combination of these mechanical variables. In many cases these functions are performed by either electric motors or generators which tend to suffer wire insulation failure in a 150ºC or 175ºC environment causing a loss of service down hole. Both of these conventional electric drives can be replaced with Turbine Dynamics patented electric mud motor technology which shifts the hot spots in normal electric drives to improve work load, performance and down hole reliability. Please call to discuss or for additional information.